Meet The Bridgewater Team
Bridgewater is highly devoted to adhering to diversity in both its supplier base and its employee base. More than 10 percent and over $250 million of the company’s annual external purchasing spending is done with minority-owned businesses. Nearly two-thirds of employees are racial minority persons. A third of the workforce is female. The management team reflects industry-leading levels of racial and gender diversity. These percentages are not the result of happenstance, but rather a concerted effort that is geared towards aggressive outreach and recruiting efforts. It is part of our mission and infrastructure.
In fact, Bridgewater is a certified Minority Business Enterprise (MBE) by the Michigan Minority Supplier Development Council, a regional affiliate of the National Minority Supplier Development Council. The company operates four manufacturing facilities, has 2,400 employees, and generates annual revenue of just over $2 billion, making it one of America’s largest Black-owned companies. Bridgewater also has the distinction of receiving the largest contracts ever awarded to an MBE by General Motors (1998), Ford (2003), and Honda (2004).
Ultimately, Bridgewater believes that only through total inclusion can the business optimize its full potential to deliver unmatched quality products to the customers it serves.
Our Leadership
Ronald E. Hall Jr.
President & CEO
David L. Viera
Chief Operating Officer
Carrie (Elaine) Tingle
Vice President,
Human Resources
and Community Affairs
John Cloud
Chief Financial Officer
Our Plant Managers
Erik Hall
Plant Manager of BWI Detroit
Johnny Collins
Plant Manager of BWI Warren
Dezi Hamilton
Plant Manager of BWI Oxford
Sheila James
Plant Manager of BWI Lansing
Meet more of our team by clicking here to see our BWI Employee Spotlight.
Our Team Pillars
Diversity
Inclusion
Potential
Resilience
Snapshot Of All BWI Plants
Employees
%
Minority
%
Female
Years Average Tenure
Years Old, Average Age
How We Work
At Bridgewater, we are focused on manufacturing the best automotive seating systems in the industry. Each of the 3,500 automotive seating systems we produce daily is the result of meticulous attention to detail that never deviates from our customers’ specifications. Part of our core competency is our Just-In-Time (JIT) expertise. A process that ensures automotive seating components arrive at our customers’ facilities on time and in the proper order, JIT production systems safeguard against potential waste.
Our Capabilities
- Sequencing and J.I.T.
- Sustainable Manufacturing and Quality Processes
- Competitive Cost Structure
- Launch Execution
- Dependable Workforce
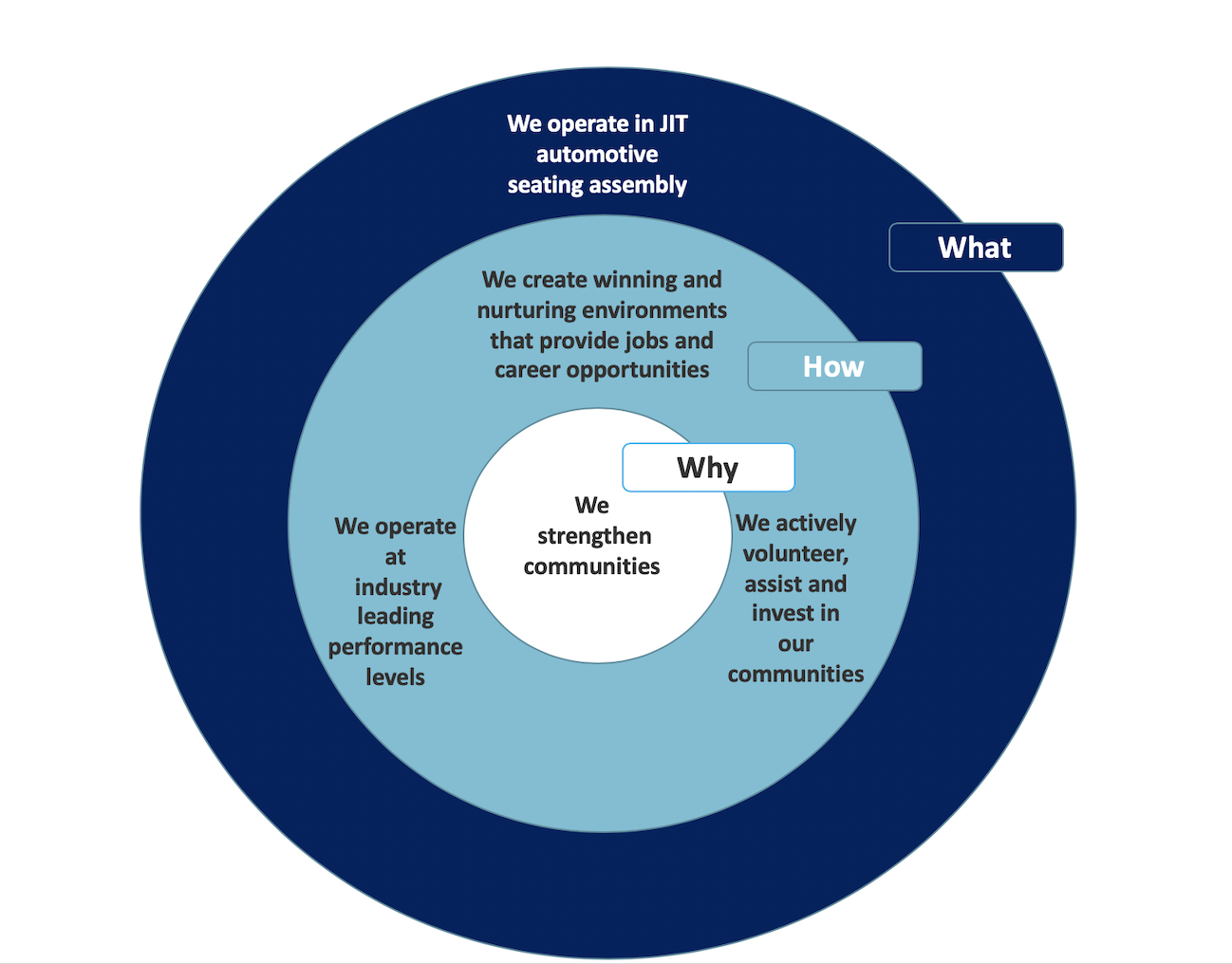